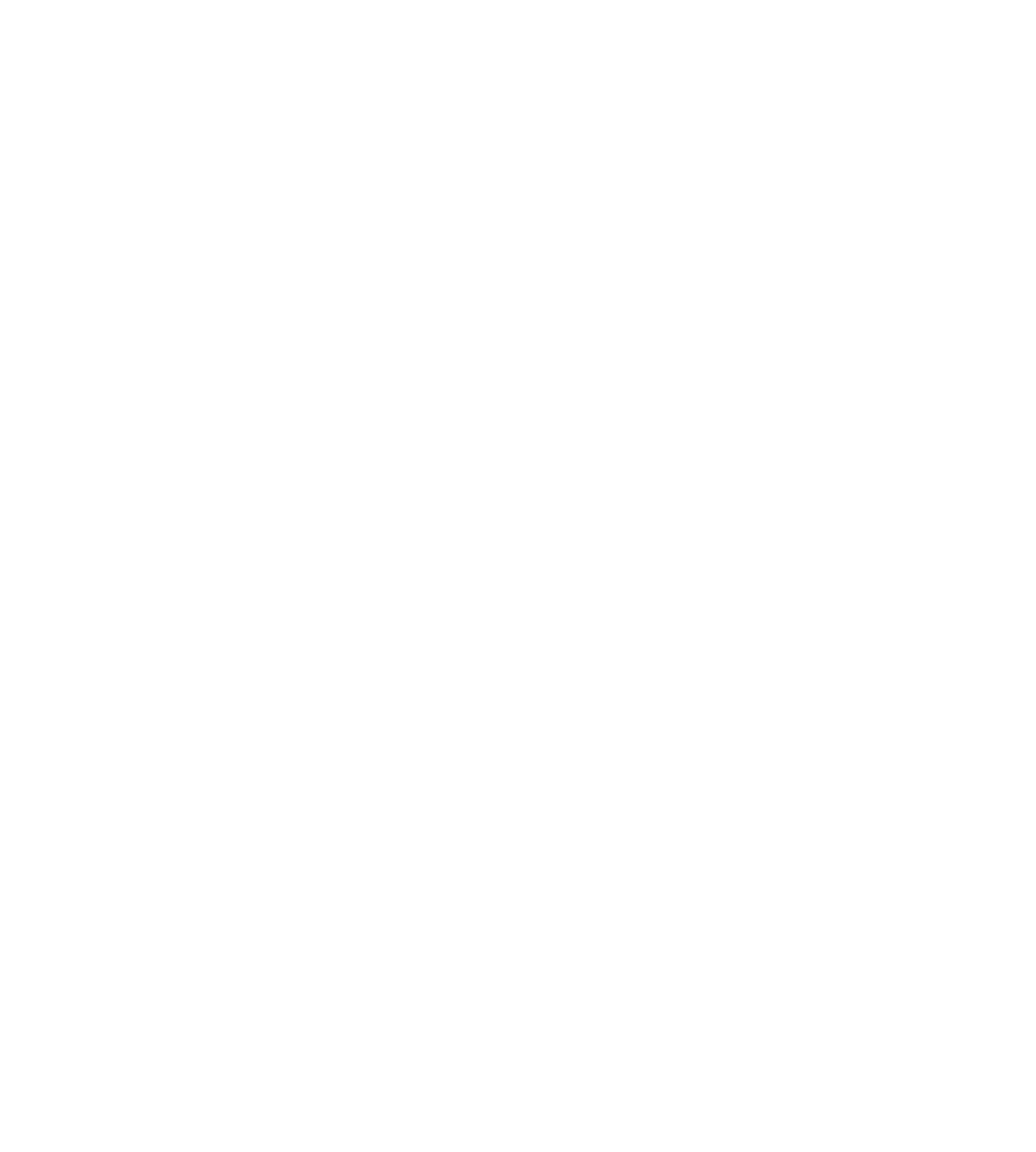
Stories from the University of Cambridge
Deployable 3D printer for soft materials
-
Yan Yan Shery Huang[1],[2], Corrado Mazzaglia[1],[2], Yaqi Sheng[1],[2], Leonor Nunes Rodrigues[3], Iek Man Lei[2], Jacqueline D. Shields[3],[4], Chon Lok Lei[1],[2], Cilian Leow[1],[2]
1 The Nanoscience Centre, University of Cambridge, Cambridge, UK 2 Department of Engineering, University of Cambridge, Cambridge, UK 3 MRC Cancer Unit, University of Cambridge, Cambridge, UK 4 Comprehensive Cancer Centre, King’s College London, London, UK
-
Shery Huang:
yysh2@cam.ac.ukCorrado Mazzaglia:
cm986@cam.ac.ukYaqi Sheng:
ys549@cam.ac.uk -
Samuel McDermott:
sjm263@cam.ac.ukPietro Cicuta:
pc245@cam.ac.uk -
Mazzaglia C, Sheng Y, Rodrigues LN, Lei IM, Shields JD, Huang YYS. 2023. Deployable extrusion bioprinting of compartmental tumoroids with cancer associated fibroblasts for immune cell interactions. Biofabrication 15, 025005. Lei IM, Sheng Y, Lei CL, Leow C, Huang YYS. 2022. A hackable, multi-functional, and modular extrusion 3D printer for soft material. Scientific Reports 12, 12294.
-
https://github.com/iekmanlei/Printer.HM
-
Cambridge Trust (UK), Chinese Scholarship Council (China), Clarendon Scholarship (UK, Engineering and Physical Sciences Research Council (UK), European Research Council (European Union), Macao Scholarship Funding (China), Medical Research Council (UK), UM Macao Fellowship (China), W.D. Armstrong Trust Fund (UK)
ABOUT THE OPEN-RESOURCE
Background
Three-dimensional (3D) printing is a technology that has rapidly gained importance in different sectors in the last decades especially due to its versatility, allowing the users to customise product designs fully. Compared to the different 3D bioprinting methods, extrusion bioprinting is the most widely used as it has a lower material usage and waste, and it can accommodate a broad range of material. Even though a lot of innovations in extrusion 3D printing have been achieved in recent years, most of the available systems are expensive and difficult to be relocated due to its bulkiness. Corrado, Research Associate in the Biointerface group, at the Department of Engineering, was interested in applying 3D printing to biomedical sciences, and he explains that, “When you work with biological material, sometimes you need to be in a sterile environment, in a biosafety cabinet, but usually bioprinters are these kind of big units.” Thinking about how to make extrusion 3D printers more accessible, the Biointerface group decided to develop a low-cost and easy to transport extrusion 3D printer.
Function
It is a deployable 3D extrusion printer for soft materials that can be folded, transported, and rapidly re-assembled, e.g., for switching between working spaces; or, for printing inside a biosafety cabinet when applying its use to biological materials that are non-transportable (due to a materials transfer agreement or ethical restrictions).
Development process
The portable 3D printer consists of a printhead controlled by Arduino (an open source electronic board with a simple microcontroller), and a robotic arm controlled by Python codes, all assembled into supporting metal frames. As the Biointerface group is highly-multidisciplinary, the deployable 3D printer was first developed for printing soft material in general. The next step was to translate the technique to biological materials, focused on cancer research. The robotic arm was then adapted to hold a Petri dish, enabling the user to generate 3D printed tumoroids. This generated tumour mass can be subsequently used for studies, with a huge potential for cancer drug testing in the near future. Yaqi, a PhD student in the Biointerface group was directly involved with the printer development and she explains that the biggest challenge for her was related to protocol optimisation, to try to achieve a satisfactory printing performance. For Corrado, on the other hand, as he
was applying the technique to the biomedical field, the challenges that he encountered were more related to the communication between the engineering and biological fields, as different areas have different strengths and drawbacks.
Target user
Researchers, especially the ones focused on studying biological material, e.g., for drug testing, or for gaining mechanistic understanding on some specific organs or tissues.
Comparison to other technologies
Compared to the commercial options, the deployable 3D printer is much more affordable, smaller, and lighter. Moreover, it is foldable, and easy to assemble, making it easy to store and transport. As the printer is open source and was built from simple components, its parts can be readily sourced and fabricated. Another advantage is that the deployable 3D printer operates with smaller volume when compared to the commercial options, making it compatible with many biological materials. Yaqi points out that portable printers have a lower mechanical resolution than commercial systems. However, the one described here is the most precise when compared to other 3D portable printers available.
IMPACT
Current use
At the moment, the deployable 3D printer has been used just by the Biointerface group and collaborators, but due to its portability and versatility, more researchers are becoming interested in it.
Successful stories
Corrado’s study in Biofabrication (additional information can be found here) is one of the examples of the potential that the 3D printer has for developing strategies in cancer drug testing. Another successful application of the system has been published in Nature Communication by Lei and collaborators (additional information can be found here), where 3D printed cochleae were used to replicate patient cochlear profiles for implant testing.
Open source choice
The main reason why the Biofabrication group decided to release the deployable 3D printer as open source was to make it more accessible, as in their field commercial equipment can be cost-prohibitive. “Since the beginning it wasn’t to commercialise something, it was more to make something new and have it available for everyone,” says Yaqi.
GOING FORWARD - WHERE TO IN THE NEXT 3-5 YEARS?
The Biofabrication group is always open to collaboration, especially in projects with potential application to the biological field.
Features of the deployable printer showing its multi-functionalities in one-platform. © 2022, Lei et al., licensed under CC-BY 4.0. Reproduced from Scientific Reports 12, 12294, doi: https://doi.org/10.1038/s41598-022-16008-6.
“Since the beginning it wasn’t to commercialise something, it was more to make something new and have it available for everyone.”
Yaqi Sheng
The deployable printer can be folded, transported, and easily re-assembled. © 2023, Mazzaglia et al., licensed under CC-BY 4.0. Reproduced from Biofabrication 15, 025005, https://doi.org/10.1088/1758-5090/acb1db.